The pi-Shaper, also known as the πShaper, is designed to transform Gaussian or similar intensity distributions of source laser beams into flat-top ones. This innovative technology has found applications in various industries due to its unique capabilities. Let’s delve into the pros and cons of pi-Shapers, explore their applications in industry, and touch upon their historical background.
The development of beam shaping optics, including pi-Shapers, has roots in the broader history of laser technology. Early experiments with beam shaping date back to the late 20th century, and over time, researchers and engineers have continually refined these techniques. The advent of pi-Shapers represents a milestone in achieving precise control over laser beam profiles, opening new possibilities for applications in various industries [1]
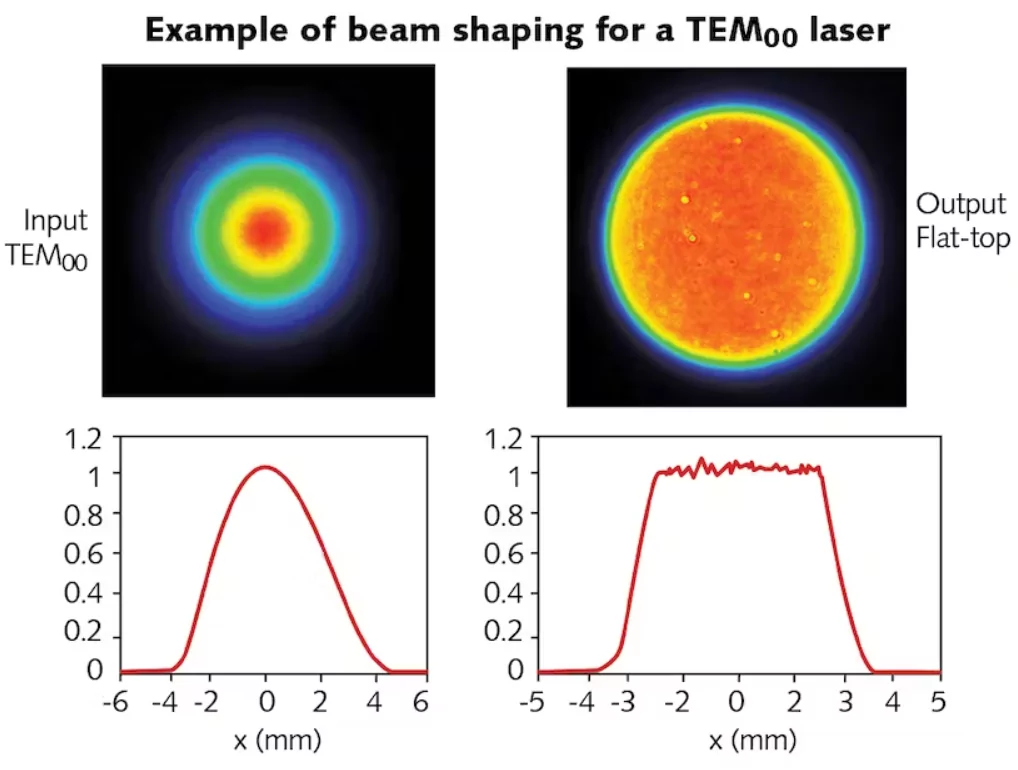
Pros of Pi-Shapers:
1. Flat-Top Beam Transformation:
The primary advantage of pi-Shapers lies in their ability to convert incoming collimated laser beams with Gaussian intensity profiles into flat-top distributions. This transformation ensures a uniform intensity across the beam profile, which is crucial for many industrial applications [4]
2. Achievement of Flat Bottom Hole Ablations:
Pi-Shapers, such as the pi-shaper from AdlOptica, are known to achieve flat bottom hole ablations in metals and silicon. This makes them valuable tools for precision material processing applications, particularly in the fabrication industry [3]
3. Compatibility with Various Source Beams:
The versatility of pi-Shapers is noteworthy as they can transform both TEM00 and multimode beams with Gaussian or similar intensity distributions into flat-top profiles. This flexibility expands their range of applications across different laser systems [4]
Cons of Pi-Shapers:
1. Complex Design:
The design of pi-Shapers can be intricate, involving specific optical elements and precise configurations. This complexity may pose challenges in terms of manufacturing and maintenance, potentially affecting their widespread adoption [1]
2. Cost Considerations:
The advanced technology and precision required for pi-Shapers contribute to their higher manufacturing costs. This cost factor may limit their accessibility to smaller enterprises or research facilities with budget constraints [4]
Applications in Industry:
1. Material Processing:
Pi-Shapers play a crucial role in laser material processing applications, including cutting, welding, and engraving. Their ability to achieve flat-top beam profiles ensures uniform processing and enhances the quality of fabricated components [3]
2. Medical Device Manufacturing:
The precision offered by pi-Shapers makes them valuable in the manufacturing of medical devices, where intricate and accurate laser processing is often required for components such as stents and surgical instruments.
3. Research and Development:
Pi-Shapers find applications in research and development environments, facilitating experiments that demand controlled and uniform laser beams. This includes studies in optics, photonics, and other related fields.
In conclusion, pi-Shapers stand as innovative devices with both advantages and challenges. Their impact on industrial processes, particularly in material processing and manufacturing, underscores their importance in modern optics. As technology advances, ongoing research and development in beam shaping optics promise even more sophisticated and accessible solutions for diverse applications.
Sources
- ResearchGate – Shaper: Refractive Beam Shaping Optics for Advanced Laser Technologies
- Optica – Beam profile shaping for laser radars that use detector arrays
- Wiley Online Library – Optical Beam Shaping: Unmet Needs in Laser Materials
- πShaper – πShaper Series
- A. Laskin et al., Proc. SPIE, 9887, 98872E (Apr. 27, 2016);